Unlocking the Secrets of Reservoir Fluids: Testing Properties and Behavior
 |
Unlocking the Secrets of Reservoir Fluids: Testing Properties and Behavior |
As reservoir pressure is reduced and liquid and gas phases are formed, one or the other of the two phases is produced differentially to some degree because of variations of permeability of the rock to gas and oil as fluid saturations change. Hydrocarbon analysis of the composite production therefore changes from that of the original material in place in the reservoir. Thus, behavior of reservoir fluids during production operations cannot be described completely by what their behavior would be under equilibrium conditions as previously described. Laboratory measurements are needed on phase behavior of reservoir fluid samples for conditions of change where liquid and gas separate both differentially and under equilibrium conditions to solve production problems involving separation under both conditions.
The practical approach to the study of reservoir fluid behavior as practiced by the industry is to anticipate pressure and temperature changes in the reservoir and at the surface during production operations; then measure by laboratory tests the changes occurring to reservoir fluid samples.
Oil Sampling and Testing
Two general methods are used to obtain samples of reservoir oil for laboratory examination purposes; (1) by means of subsurface samplers and (2) by obtaining surface samples of separator liquid and gas. Separator samples of oil and gas are recombined in the laboratory in proportions equivalent to the gas-oil ratio measured at the separator.
Data usually obtained include: (1) original reservoir temperature and pressure; (2) pressure-volume relations at one or more temperatures, one of which is always the reservoir temperature (taken as shown in the next figure); (3) effects of variation of surface separator pressure on amounts of gas liberated and shrinkage of oil resulting from such separation process; (4) differential gas liberation and oil shrinkage data, taken in the manner shown in next figure; (5) density or specific volume of reservoir fluid; (6) viscosity relation of reservoir oil at reservoir temperature and at pressures ranging from original reservoir pressure to atmospheric pressure and viscosity of stock tank oil; (7) hydrocarbon and orsat analyses of the mixture as it existed originally in the reservoir; and (8) ASTM distillation analyses of residual oil.
 |
Laboratory equilibrium liberation (P.V.T) of gas from oil |
 |
Laboratory differential liberation of gas from oil |
Equilibrium and Differential Data of Oil Samples
If liberated gas is permitted to stay in direct contact with a liquid sample, a different volume of gas will be liberated down to a given pressure, then would be released if the gas were removed from contact with the liquid as it is liberated. The remaining liquid is likewise different in the opposite direction; thus, oil shrinkage is different. Differential liberation is that process which takes place when the gas is removed as it is formed incident to a drop in pressure at constant temperature. Each type of liberation process is encountered to some degree at one time or another in the production of petroleum deposits; therefore, both processes for a given oil sample must be investigated to provide data for a complete reservoir study.
A comparison of equilibrium and differential shrinkage of a low shrinkage oil under reservoir conditions as pressure drops is presented in the next figure. This shows that, under equilibrium conditions, a greater quantity of heavy components is progressively pulled into the gas by the light gas components; thus, oil shrinkage is greater. Lower shrinkage by differential liberation under these conditions is caused by gas being removed as it is formed, thereby preventing further attraction of light gas molecules to heavy liquid molecules, and minimizing the quantity of liquid pulled into the gas phase.
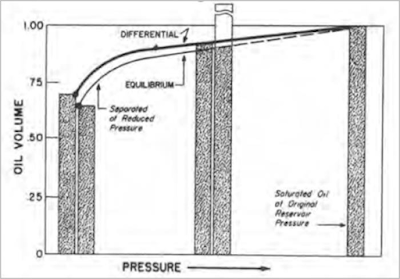 |
Equilibrium and differential shrinkage of low shrinkage oil |
 |
Equilibrium and differential shrinkage of high shrinkage oil |
A comparison between equilibrium and differential shrinkage of a very high shrinkage oil is presented in the above figure. In this case, the difference is reversed from that of low shrinkage oil. More gas is formed in the high-pressure range than with low shrinkage oil. This is caused by a large quantity of intermediates being pulled into the gas phase (through great attraction to the densely spaced light gas molecules and through high kinetic energy of the intermediates). Once the large quantity of intermediates is removed from the system by differential liberation, they have no further influence on gas liberation and oil shrinkage; therefore, oil shrinkage remains high through lower pressure ranges. If the gas is not removed, as in flash or equilibrium liberation, some intermediate gas molecules may condense because their attraction to light gas molecules is reduced as pressure drops and the light gas molecules become farther apart; thus, vaporizing tendency of high shrinkage oil may be reversed until shrinkage is less under equilibrium conditions than under the differential process.
Shrinkage curves of both low and high shrinkage oil illustrate that, near atmospheric temperature and low-pressure conditions, shrinkage of oil greatly increases and presents a problem if maximum liquid volume is to be produced to the stock tank as saleable material.
Oil of all degrees of shrinkage will shrink less to the stock tank if the material is first passed to a separator at some elevated pressure and free gas, formed down to that pressure and temperature, is separated. Also, there is an optimum separator pressure condition where minimum shrinkage of oil is obtained.
Gas Sampling and Testing
Free gas is classified into three general types according to phase behavior upon reduction of temperature or pressure (or both) as illustrated by the phase diagrams in the next figures. The types are termed retrograde condensate gas, wet gas and dry gas, respectively, and may apply to gas deposits that are either associated or non-associated with oil deposits.
There are two general methods for sampling gas wells. The first utilizes the full-scale field separator and involves recombination of separator material in the laboratory for testing. The second method uses a tubing head (or line probe) which diverts a portion of produced material to a mobile small-scale separator, portable laboratory or test car which involves performing part of the tests in the field on large samples. Use of the latter method is generally limited to detailed testing of retrograde condensate gas reservoirs.
Information concerning the characteristics and behavior of gas most frequently needed for work with gas reservoirs depends upon the types of gas considered and the nature of the problem. If the problem at hand involves retrograde condensation as pressure drops, the information needed may become very complex and may require numerous tests and measurements. If the problem involves wet gas (where no retrograde condensation occurs but liquid is recovered in separators) or dry gas (where no liquid is condensed in either the reservoir or separator), then the information needed may be considerably less complex.
Retrograde condensate gas material will be described here. It is important that enough tests be made on gas produced from gas reservoirs to identify the gas positively as to its retrograde characteristics in order for the operator to guard against losing economically recoverable liquids. Laboratory data of condensate gas reservoir fluids include data on (1) the quantity, hydrocarbon analysis and specific volume of original material in the reservoir, (2) the quantities of vapor and condensed liquid in the reservoir at subsequent reduced reservoir pressures and (3) the complete surface separation history as reservoir pressure decreases, including optimum separation data together with hydrocarbon analyses of separator gas, separator liquid, stock tank gas and stock tank liquid.
Equilibrium and Differential Data of Gas Samples
If pressure is dropped on a gas sample by increasing the volume without withdrawing gas, a different volume of liquid will drop out by retrograde condensation than will occur if pressure is dropped by removing gas without changing the volume of the remainder of the sample.
The first process, illustrated in the following figure, is termed equilibrium condensation. The latter process, illustrated in the figure that follows, is termed differential condensation and is analogous to production from a closed reservoir.
A comparison of equilibrium and differential condensation of a retrograde gas as measured in the laboratory is presented in the following figure. More liquid condenses under equilibrium conditions than under differential conditions because a greater quantity of gas remains in the system in the equilibrium process from which heavy components may condense as pressure drops.
 |
Equilibrium retrograde condensation of liquid from gas. |
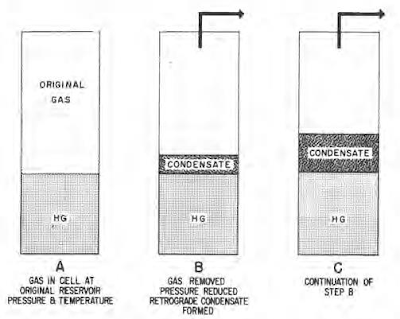 |
Differential retrograde condensation |
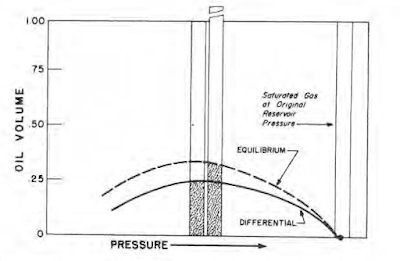 |
Differential and equilibrium condensation of liquid from gas |
Condensate Gas Problems
The important problem in condensate gas reservoir material lies in the change of composition of produced material brought about by retrograde condensation in the reservoir of the heavier hydrocarbon components as reservoir pressure drops during production operations. Retrograde condensation characteristics drastically affect desirable operations because it is the condensate material that provides a large part of the income from the produced gas. Ultimate loss of income results if liquids are allowed to condense in the reservoir to form a non-recoverable liquid saturation. Because this liquid saturation is small in percent of reservoir pore volume, its displacement from the reservoir other than adjacent to the wellbore may be difficult to accomplish by conventional production of reservoir gas.
The problem of surface separation is involved in the production of gas just as in oil production, whether reservoir conditions at the time of production are at the original or some reduced pressure. It is necessary, therefore, to establish proper separation conditions to recover a maximum amount of liquids in the separator. Obtaining maximum profits from production of gas reservoirs requires solution of these problems.
keywords: fluid, behavior, testing, properties.
Comments